How 200 machines are being maintained Axel Månsson A/S
At Axel Månsson A/S, many machines need to be maintained. Here we explain how Trendlog’s Maintenance Planner helps solve this challenge.
Axel Månsson A/S is one of Denmark’s largest producers and has been delivering vegetables to Danish kitchens for over 40 years. They are based in Brande, where they have no less than 1,900 hectares, the majority of which is produced organically. With such a large area, no less than 200 machines are needed to maintain the sustainable and organic production. This also means that they have to replace many of their machines and spare parts along the way.
By using Trendlog’s solution, the Maintenance Planner, they have been able to increase efficiency in production.
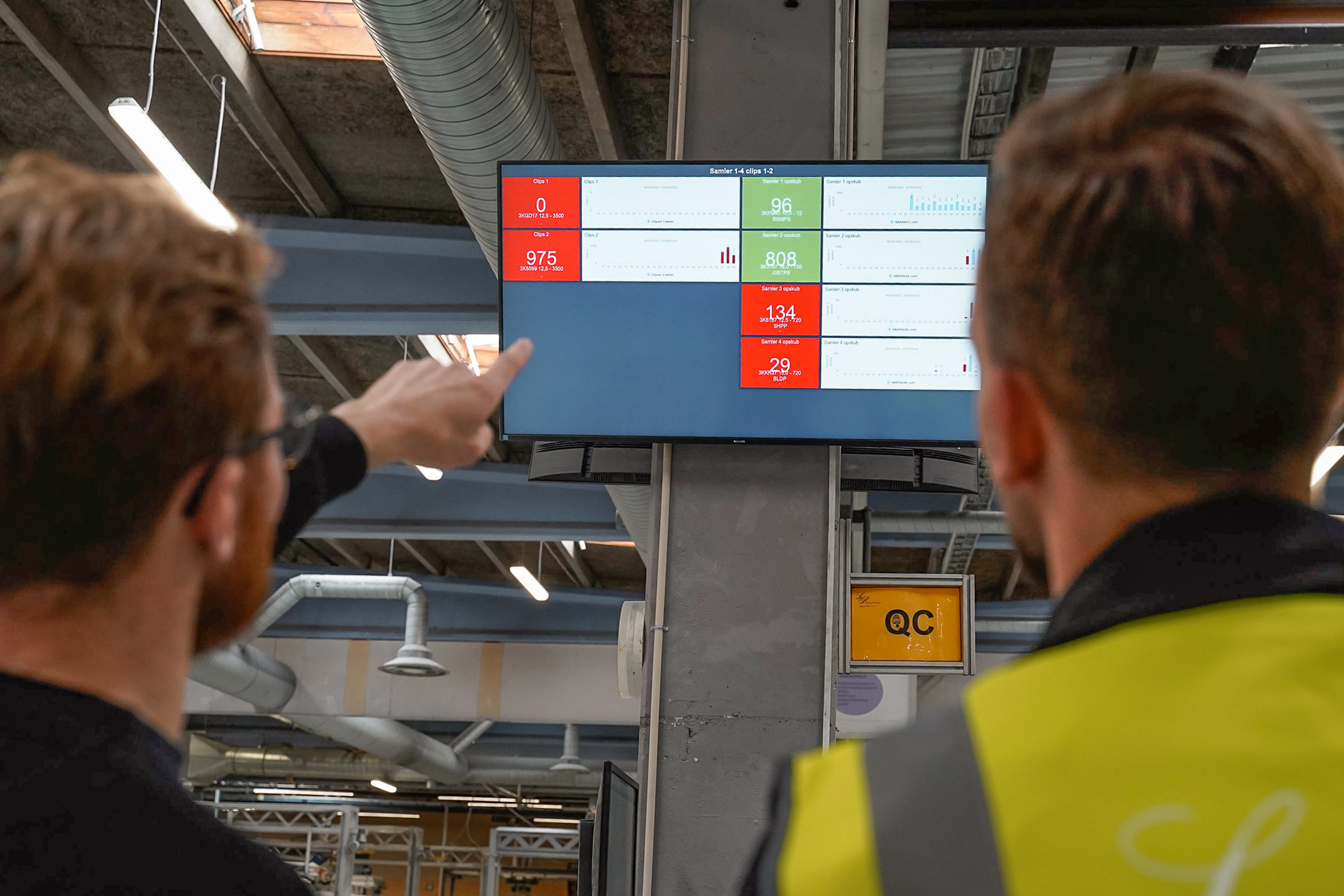

At Axel Månsson, Trendlog’s Maintenance Planner helps keep track of their tractors, scales and machinery for sorting, handling and packing organic vegetables, and for each unit a checklist of tasks is described that are important to cover to ensure continued production.
Operations and Production Manager Jonas Lauth Pedersen says.
– We are more than happy with Trendlog’s solution. It has helped us a lot to optimise our processes around production and it gives us the awareness to create change.
For Axel Månsson A/S, machine downtime means a waste of money. That’s why the Maintenance Planner is particularly important. But what does it actually do?
To predict the need for maintenance of machinery such as sorting plants or flow packs, the system needs an operational signal. The operating signal will indicate to which extent the unit is exposed to wear and tear. It will also be used to determine uptime and breakdowns. From the start, some interval points are specified at which the device should undergo a check.
For this, the system continuously measures, for example, the last month’s development and calculates when the next interval point is reached for the unit in question, and thus when a service check is due.
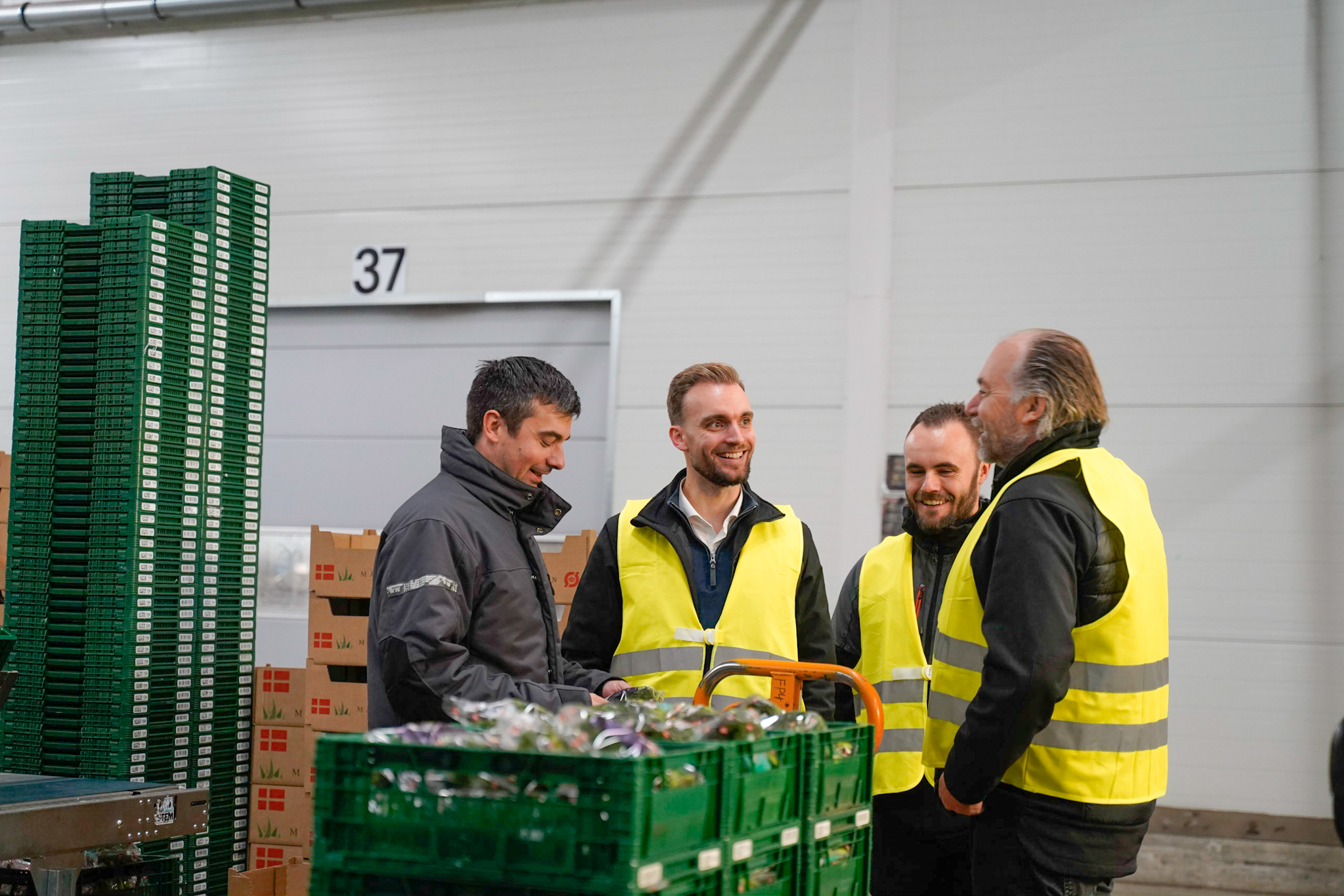