Vegetable producer prevents breakdowns with data
It takes 8 workers to control the flowpacker, which means that stoptime is the same as flushing money down the drain! So to bring that down is incredibly important to us.
In your busy everyday life it can be hard to keep track of the machinery and gears keeping the production going. For most corporations, the manufacturing and quality of the product they make is the most important thing. Danish vegetable producer Månsson are using the maintenance system Maintenance Planner to keep track of machines and installations, which is why they no longer forget the tractor in the corner.
The operations manager Jonas explains how other corporations can benefit from the same system.
Månsson has been testing our Maintenance Planner through a pilot project, which has been going for over six months. You can read about the project in this case story.
Axel Månsson A/ S produces vegetables and eggs in large amounts right from the field to the store. Therefore they have a fleet of tractors, large vehicles, handling facilities and production machinery which needs maintenance to not risk breakdowns and falling behind.
From the early stages of the process and until now, they have registered over 200 different production units, which the systems keeps track of in means of maintenance and inspections. And the fact that the system can handle a large and widespread fleet is very important to the production manager, Jonas Pedersen:
– We can be completely sure of the fact that all units will be followed up on. You can see how many machines we have here, right? And it will keep growing like that. We have 66 tractors now, but in 2-3 years we’ll have 70 or 80, and that’s the deal with all of our machines. That’s why it’s important to keep track of all things and not forget the machine in the corner.
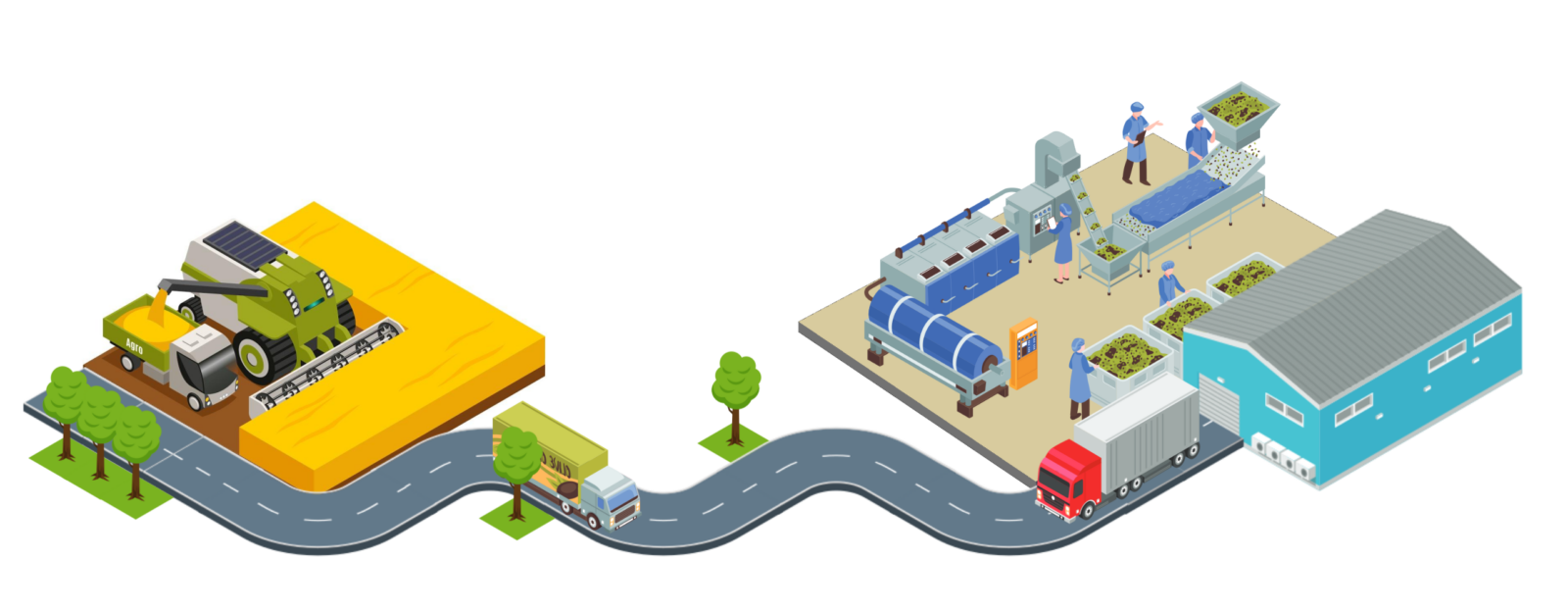
The maintenance plan keeps track of Månssons tractors, weighers and machinery for sorting, handling and packing of organic vegetables. And for every unit there is a checklist of tasks, which are important to complete in order to ensure the continued production.
Fact box
How does Maintenance Planner predict maintenance?
To predict the machinery’s need for maintenance, such as sorting installations or flow packers, the system will need an operating signal. The operating signal will indicate to which extent the unit is exposed to wear and tear. It will also be used to determine uptime and breakdowns. From the start, interval points, (for example at 50.000 produced units) which will indicate when the unit need to go through a checkup for various elements such as gears, oil, pressure and so on. Furthermore, the system will continuously measure the development and calculate when the next interval point will be reached, and a service check-up must be performed.
“Stoptime is money down the drain“
The system automatically keeps an eye on upcoming service jobs, so that when it’s time for a service check-up, a message will be sent beforehand to the technician or operating manager, Jonas has chosen and appointed.
– I just look at: how many service check-ups do I have left? And then I have to check up on my workshop crew if it’s outside, or my technician-team if it’s inside (red: tractors vs. production machinery). That’s where I use the system as a management tool. And now it’s their job to make sure the service logs from check-ups etc. are up to date.
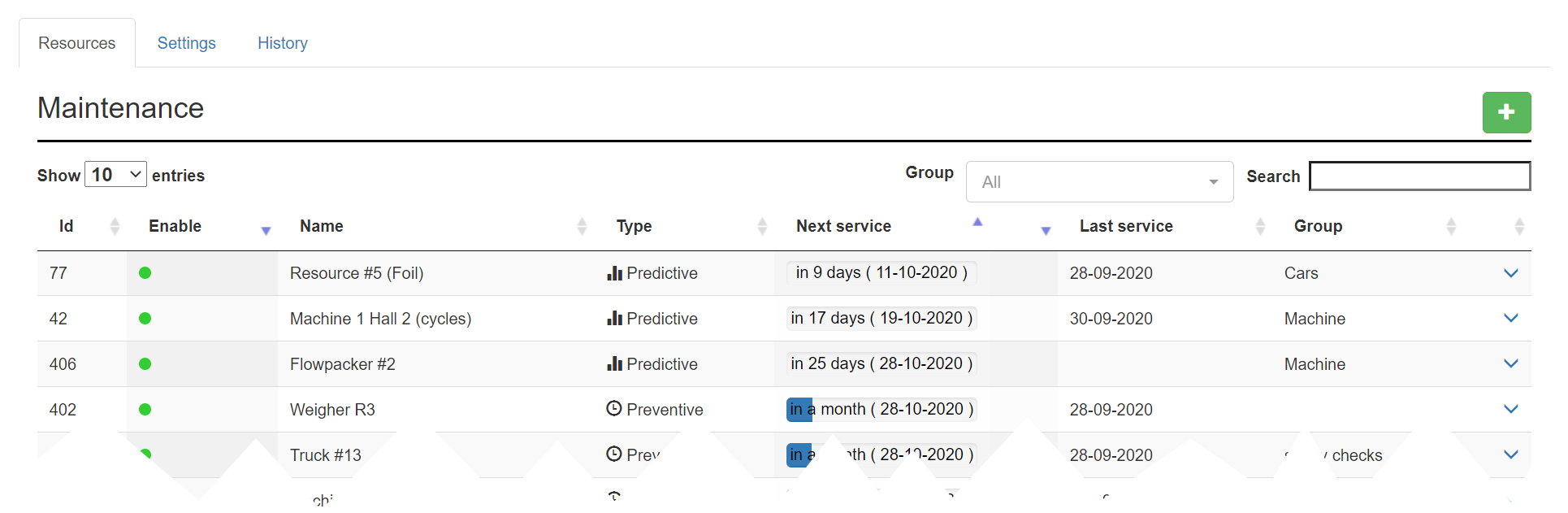
The combination of the system, which automatically notifies the technician or operating manager, and the continuous service check-ups completed by the technicians on the basis of fixed checklists, is important to make sure operating manager Jonas can keep an effective flow of production:
– Instead of falling behind, we perform preventive maintenance, which is why we are starting to see certain tendencies of different wear parts. For example, we measure how many times the knives on flowpackers cut. Because, if we can replace it before it breaks, we can save valuable time. It takes 8 workers to control the flowpacker, which means that stoptime is the same as flushing money down the drain! So to bring that down is incredibly important to us.
Prevents breakdowns with data
To both the manager Jonas and the employees at Månsson, the fact that they can prevent breakdowns and can anticipate maintenance and fix serious problems as they come, brings great value to their daily life at Månsson.
– That’s what’s most important to us. Not forgetting anything and making sure to get ALL machines through the workshop, instead of some machines not being checked and put away for ages. And sometimes there have been faulty machines that haven’t been fixed. Now, everything is checked thoroughly and ready for the driver or operator as we go.
The organic vegetable producer has not only reduced their maintenance costs immensely. They have also saved their worries by letting Jonas and his employees focus on their most important job: delivering organic vegetables of the highest quality to Danish homes.
Once again we would like to extend our gratitude towards Axel Månsson for participating in our pilot project and towards Jonas for the excellent feedback on the system.
If you want to know more about Maintenance Planner, keep reading here.
If you want to try maintenance planning at your company, you are more than welcome to contact us for a test run.
Others also read
Great success on Automatica
Last week, a large part of the Trendlog team was in Munich at the Automatica 2022 trade fair, where we were part of Odense Robotics’ Danish pavilion. And what a week it was!
Trendlog.io presents new CEO
Per 1st of October, Trendlog.io restructured internally, and has assigned Sebastian Märcher Sandig as new CEO.
The all-new Trendlog Collect 2.0
The all-new Trendlog Collect 2.0 – The simple way of optimizing production.